机器人驱动介绍
其他
2018-12-04 10:00:59
阅读次数: 0

电气驱动是利用各种电动机产生的力或力矩,直接或经过减速机构去驱动机器人的关节,以获得要求的位置、速度和加速度。电气驱动具有无环境污染、易于控制、运动精度高、成本低、驱动效率高等优点,应用最为广泛,电气驱动可分为步进电机驱动、直流伺服电机驱动、交流伺服电机驱动、直线电动机驱动。交流伺服电机驱动具有大的转矩质量比和转矩体积比,没有直流打击的电刷和整流子,因而可靠性高,运行时几乎不需要维护,可用在防爆场合,因此在现代机器人中广泛应用。
电气驱动是利用各种电动机产生的力或力矩,直接或经过减速机构去驱动机器人的关节,以获得要求的位置、速度和加速度。电气驱动具有无环境污染、易于控制、运动精度高、成本低、驱动效率高等优点,应用最为广泛,电气驱动可分为步进电机驱动、直流伺服电机驱动、交流伺服电机驱动、直线电动机驱动。交流伺服电机驱动具有大的转矩质量比和转矩体积比,没有直流打击的电刷和整流子,因而可靠性高,运行时几乎不需要维护,可用在防爆场合,因此在现代机器人中广泛应用。
步进电动机是一种用电脉冲信号进行控制,将电脉冲信号转换成相应的角位移或线位移的控制电动机。由于步进电动机的步距或转速,不受电压波动和负载变化的影响,不受环境条件的限制,仅与脉冲频率同步,能按控制脉冲的要求立即启动、停止、反转或改变转速,它每一转都有固定的步数,在不丢步的情况下运行时,步距误差不会长期积累,因此,它不仅在闭环系统中作控制元件,而且在程序控制系统中作开发控制和传动元件用时能大大简化系统。
① 永磁式步进电动机 它是一种由永磁体建立励磁磁场的步进电动机,也称永磁转子型步进电动机。其缺点是步距大,启动频率低;其优点是控制功率小,在断电情况下有定位转矩。步进电动机可以制成多相,通常有一相、两相和三相。
如图5-17所示。转子为一对极或几对级的星型磁钢,定子上有两相或多相绕组,定子每相的轴线相对于转子的轴线,这类电动机要求电源提供正负脉冲。
当定子绕组A相正向通电时,在定子A相的A(1)、A(3)端产生S极,而A(2)、A(4)产生N极,由磁极性质,转子位于图5-17(a)的位置上;当A相断电B正向通电时,定子B向的B(1)、B(3)端产生S极,而B(2)、B(4)产生N极,转子顺时针旋转45°至图5-17(b)位置;当B相断电,A相负向通电时,定子A相的A(1)、A(3)端产生N极,而A(2)、A(4)产生S极,转子再顺时针转45°至图5-17(c)位置;当A相断电B相负向通电时,定子B相的B(1)、B(3)端产生N极,而B(2)、B(4)产生S极,转子再顺时针旋转45°至图5-17(d)位置。
依次按上述A→B→A→B单四拍方式通电,转子便连续旋转,也可按双四拍的方式AB→BA→AB→BA通电,步距角均为45°,若按A→AB→B→BA…八拍方式通电,则旋转步距为角为22.5°。
要减小步距角,可以增加转子的磁极数及定子的齿数, 但转子要制成N-S相间的多对磁极是很困难的,同时,定子级数及绕组线圈数也必须相应的增加,这将受到定子空间的限制,因此永磁式步进电动机的步距角都较大。
② 反应式步进电动机 它是一种定、转子磁场均由软磁材料制成,只有控制绕组,基于磁导的变化产生反应转矩的步进电动机,又称为变磁阻步进电动机。它的结构按绕组的顺序可分为径向分相和轴向分相。按铁芯分段,则有单段式和多段式。
③ 永磁感应子式步进电动机 它的定子结构与反应式步进电机相同,而转子由环形磁钢和两段铁芯组成,它与反应式步进电机一样,可以使其具有小步距和较高的启动频率,同时又有永磁式步进电动机控制功率小的优点。其缺点是由于采用的磁钢分成两段,致使制造工艺和结构比反应式步进电动机复杂。
直流伺服电动机是用直流供电的电动机。其功能是将输入的受控电压/电流能量转换为电枢轴上的角位移或角速度输出。其结构如图5-24所示,它由定子、转子(电枢)、换向器和机壳组成。定子的作用是产生磁场,转子由铁芯、线圈组成,用于产生电磁转矩;换向器由整流子、电刷组成,用于改变电枢线圈的电流方向,保证电枢在磁场作用下连续旋转。
稳定性好,它具有较好的机械性,能在较宽的速度范围内运行。
可控性好。它具有线性调节的特性,能使转速正比于控制电压的大小;转向取决于控制电压的极性(或相位);控制电压为零时,转子惯性很小,能立即停止。
相应迅速。它具有较大的启动转矩和较小的转动惯量,在控制信号增加、减小或消失的瞬间,能快速启动、增速、减速及停止。
转矩大。直流伺服电动机广泛应用在宽调速系统和精确位置控制系统中,其输出功率为1-600W,电压有6V、9V、12V、24V、27V、48V、110V、220V等,转速可达1500-1600r/min。
直流伺服电动机用直流供电,为调节电动机转速和分享需要对其直流电压的大小和方向进行控制。目前常用晶体管脉宽调速驱动和可控硅直流调速驱动两种方式。可控硅直流驱动,主要通过调节触发装置控制可控硅的导通角(控制电压的大小)来移动触发脉冲的相位,从而改变整流电压的大小,使直流电动机电枢电压的变化易于平滑调速。由于可控硅本身的工作原理和电源的特点,导通后是利用交流(50Hz)过零来关闭的,因此在低整流电压时,其输出时很小的尖峰值的平均值,从而造成电流的不连续性。而采用脉宽调速驱动系统,其开关频率高,赐福机构能够相应频带范围也比较宽。与可控硅相比,其输出电流脉动非常小,接近于纯直流。
(1)同步型(SM)采用永磁结构的同步电动机,又称为无刷直流伺服电动机。其特点为:
其特点为: ① 对定子电流的激励分量和转矩分量分别控制; ② 具有直流伺服电动机的全部优点。
式中n-电动机转速 f-电源电压频率 p-电动机磁极对数
n0=60f/p 电动机定子旋转磁场转速或称同步转速
改变磁极对数p调速,一般所见的交流电动机磁极对数不能改变,磁极对数可变的交流电动机成为多速电动机。通常,磁极对数设计成4/2, 8/4, 6/4, 8/6/4等几种。显然磁极对数只能成对改变,转速只能成倍改变,速度不可能平滑调节。
改变转差率S调速。此办法只适用于绕线式异步电动机,在转子绕组回路中串入电阻使电动机进机械特性变软,转差率增大。串入电阻越大,转速越低,调速范围通常为3:1.
改变频率f调速。如果电源频率能平滑调节,那么速度也就可能平滑改变。目前,高性能的调速系统大都采用这种方法,设计了专门为电动机供电的变频器VFD。
目前直线电动机主要应用的机型有直线感应电动机、直线直流电动机和直线步进电动机三种。
直线电动机由于不需要中间传动机械,因而使整个机械得到简化,提高了精度,减少了振动和噪声。 l 快速响应。用直线电动机驱动时,由于不存在中间传动机构惯量和阻力矩的影响,因而加速和减速时间短,可实现快速启动和正反向运行。
仪表用的直线电动机,可省去电刷和换向器等易损零件,提高可靠性,延长寿命。
直线电动机由于散热面积大,容易冷却,所以允许较高的电磁负荷,可提高电动机的容量定额。
装配灵活性大,可将电动机和其他机件合成一体。 (1)直线感应电动机(LIM)
直线感应电动机可以看做是由普通的旋转感应电动机直接演变而来的。图5-28(a)表示一台旋转的感应电动机,设想将它沿径向剖开,并将定、转子沿圆周方向展出直线,如图5-28(b),这就得到了最简单的平板型直线感应电动机。由定子演变而来的一侧称为初级,由转子演变而来的一侧称作次级。直线电动机的运动方式可以是固定初级,让次级运动,此称为动次级;相反,也可以固定次级而让初级运动,则称为动初级。
图5-29中直线电动机的初级和次级长度是不等的。因为初、次级要作相对运动,假定在开始时初、次级正好对齐,那么在运动过程中,初、次级之间的电磁耦合部分将逐渐减少,影响正常运行。因此在实际应用中,必须把初次级作的不等。其他几种形式:
直线直流电动机(LDM)主要有两种类型:永磁式和电磁式。永磁式推力小,但运行平稳,多用在音频线圈和功率较小的自动记录仪表中,如记录仪中笔的纵横走向的驱动,摄影中快门和光圈的操作机构,电表试验中探测头,电梯门控制器的驱动等;电磁式驱动功率较大,但运动平稳性不好,一般用于驱动功率较大的场合。
作为LDM,以永磁式、长行程的直线直流无刷电动机(LDBLM)为代表,如图5-34所示。
当需要功率较大时,上述直线电动机中的永久磁铁所产生的磁通可改为由绕组通入直流电励磁所产生,这就称为电磁式直线直流电动机。如图5-35所示。
直线步进电动机如图5-36所示,定子用磁铁材料制成,称其为定尺。其上开有矩形齿槽,槽中填充非磁性材料,使整个定子表面非常光滑。动子上装有两块永久磁钢A和B,每一磁极端部装有用磁铁材料制成的P形极片。每块极片有两个齿(如a和c),齿距为1.5t,这样当齿a与定子齿对齐时,齿c便对准槽。同一磁钢的两个极片间隔的距离刚好使齿a与a’能同时对准定子的齿,即它们的间隔是加kt,k代表任意整数。
磁钢B与A相同,但极性相反,它们之间距离等于(k±1/4)t。这样,当其中一个磁钢的齿完全与定子齿和槽对齐时,另一磁钢的齿则应处在定子的齿和槽的中间。
在磁钢A和B的两个P形极片上分别装有控制绕组。如果某一瞬间,A相绕组中通入直流电流Ai,并假定箭头指向左边的电流为正向,如图5-36(a)所示。这时A相绕组所产生的磁通在赤a、a’中与永久磁钢的磁通相叠加,而在赤c、c’中却相抵消,使齿c、c’全部去磁,不起任何作用。在这过程中B相绕组不同电流,即ib=0,磁钢B的磁通量在齿d、d’和b、b’中大致相等,沿着动子移动方向各齿产生的作用力互相平衡。
概况说来,这时只有齿a、a’起作用,它使动子处在如图5-36(a)的位置,为了使动子向右移动,这就是说从图5-36(a)移动到图5-36(b)的位置,就要切断加在A相绕组的电源,使ia=0,同时给B相肉阿祖通入正向电流ib。这时在齿b和b’中,B相绕组产生的磁通与磁钢的磁通相叠加,而在齿d、d’却相抵消。因而,动子便向右移动半个齿宽即t/4,使齿b和b’移动到与定子齿相对齐的位置。如果切断电流Bi并给A相绕组通上反向电流,则A相绕组及磁钢上产生的磁通在c、c’中相叠加,而在d、d’中相抵消。动子便又向右移动t/4,使齿c、c’与定子齿相对齐,见图5-36(c)。
同理,如切断电流ia,给B相绕组通上反向电流,动子又向右移动t/4,使齿d和d¢与定子齿对齐,见图5-36(d)。这样,经过图5-36(a)、(b)、(c)、(d)所示的4各阶段后,动子便向右移动了一个齿距t,如果还需要移动,只需要重复前面的次序通电即可。
电液伺服系统通过电气传动方式,将电气信号输入系统来操纵有关的液压控制元件动作,控制液压执行元件使其跟随输入信号而动作。这类伺服系统中电液两部分之间都采用电液伺服阀作为转换元件。电液伺服系统根据物理量的不同可分为位置控制、速度控制、压力控制和电液伺服控制。
电液伺服系统通过电气传动方式,将电气信号输入系统来操纵有关的液压控制元件动作,控制液压执行元件使其跟随输入信号而动作。这类伺服系统中电液两部分之间都采用电液伺服阀作为转换元件。电液伺服系统根据物理量的不同可分为位置控制、速度控制、压力控制和电液伺服控制。
图5-1所示为机械手手臂伸缩电液伺服系统原理图。它由电液伺服阀1,液压缸2,活塞杆带动的机械手臂3、电位器4,步进电机5、齿轮齿条6和放大器7等元件组成。当数字控制部分发出一定数量的脉冲信号时,步进电动机带动电位器4的动触头转过一定的角度,使动触头偏移电位器中位,产生微弱电压信号,该信号经放大器7放大后输入电液伺服阀1的控制线圈,是伺服阀产生一定的开口量,假设此时压力油经伺服阀进入液压缸左腔,推动活塞连同机械手手臂上的齿条相啮合,手臂向右移动时,电位器跟着作顺时针方向旋转。当电位器的中位和动触头重合时,动触头输出的电压为零,电液伺服阀失去信号,阀口关闭,手臂停止运动,手臂的行程决定于脉冲的数量,速度决定于脉冲的频率。当数字控制部分反向发出脉冲时,步进电机向反方向转动。手臂便向左移动。由于机械手手臂移动的距离与输入电位器的转角成比例,机械手手臂完全跟随输入电位器的转动而产生相应的位移,所以它是一个带有反馈的位置控制电液伺服系统。
液压伺服驱动系统由液压源、驱动器、伺服阀、传感器和控制回路组成。
如图5-2所示。液压泵将压力油供到伺服阀,给定位置指令值与位置传感器的实测值之差经放大器放大后送到伺服阀。当信号输入到伺服阀时,压力油被供到驱动器并驱动载荷。当反馈信号与输入指令值相同,驱动器便停止。伺服阀在液压伺服系统中是不可缺少的一部分,它利用电信号实现液压系统的能量控制。在响应快、载荷大的私服系统中往往采用液压驱动器,原因在于液压驱动器的输出力与重量比最大。
电液伺服阀是电液伺服系统中的放大转换元件,它把输入的小功率电流信号,转换并放大成液压功率输出,实现执行元件的位移、速度、加速度及力的控制。
电液伺服阀通常由电气®机械转换装置、液压放大器和反馈(平衡)机构三部分组成。电气机械转换装置用来将输入的电信号转换为转角或直线位移输出。输出转角的装置称为力矩马达,输出直线位移的这装置称为力马达。
液压放大器接受小功率的电气®机械转换装置输入的转角或直线位移信号,对大功率的压力油进行那个调节和分配,实现控制功率的转换和放大。反馈和平衡机构是电液伺服阀输出的流量或压力获得与输入信号成比例的特性。
图5-3为喷嘴挡板式电液伺服阀的工作原理。图中上半部分为力矩马达,下半部分为前置级(喷嘴挡板)和主滑阀。当没有电流信号输入时,力矩马达无力矩输出,与衔铁5固定在一起的挡板9处于中位,主滑阀阀芯亦处于中(零)位。液压泵输出的油液以及压力Ps进入主滑阀阀口,因阀芯两端台肩将阀口关闭,油液不能进入A,B口,但经过固定节流孔10和13分别引到喷嘴8和7,经喷射后液流流回油箱。由于挡板处于中位,两喷嘴与挡板的间隙相等,因而油液流经喷嘴的液阻相等,则喷嘴前的压力1p与2p相等,主滑阀的阀芯两端压力相等,阀芯处于中位。若线圈输入电流,控制线圈中将产生磁通,使衔铁上产生磁力矩。当磁力矩为顺时针方向时,衔铁连同挡板一起绕弹簧管中的支点顺时针偏转。图5-3中左喷嘴8的间隙减小、右喷嘴7的间隙增大,即压力1p增大,2p减小,主滑阀阀芯在两端压力差的作用下向右运动,开启阀口,sp与B相通,A与T相通,在主滑阀阀芯向右运动的同时,通过挡板下边的弹簧杆11的反馈作用使挡板向逆时针方向偏转,使做喷嘴8的间隙增大,右喷嘴7的间隙减小,于是压力1p减小,2p增大。当主滑阀阀芯向右移动到某一位置,由两端压力差1p-2p形成的液压力通过反馈弹簧杆作用在挡板上的力矩、喷嘴液流压力作用在挡板上的力矩以及弹簧管的反力矩之和与力矩马达产生的电磁力矩相等时,主滑阀阀芯受力平衡,稳定在一定的开口下工作。
显然,可以改变输入电流的大小,可成比例地调节电磁力矩,从而得到不同的主阀开口大小。若改变输入电流方向,主滑阀阀芯反向位移,可实现液流的反向控制。图5-3中主滑阀阀芯的最终工作位置是通过挡板弹性反力反馈作用达到平衡的,因此称之为力反馈式。除力反馈之外还有位置反馈、负载流量反馈、负载压力反馈等。
电液比例控制是介于普通液压阀的开关控制和电液伺服控制之间的控制方式。它能实现对液流压力和流量连续地、按比例的跟随控制信号而变化。因此,因此它的控制性能优于开关控制,它与电液伺服控制相比,其控制精度和相应速度较低。因为它的核心元件是电液比例阀,所以简称比例阀。
图5-4所示为一直弄个电液比例压力阀的结构示意图。它由压力阀1和马达2两部分组成,当力马达的线圈通入电流I时,推杆3通过钢球4.弹簧5把电磁推力传给锥阀6.推力的大小与电流I成正比,当阀进油口P处的压力油作用在锥阀上的力,油液通过阀口由出油口排出,这个阀的阀口开度是不影响电磁推力的,但当通过阀口的流量变化时,由于阀座上的小孔d处压差的改变以及稳态液动力的变化等,被控制的油液压力依然有一些改变。
电液比例换向阀一般由电液比例减压阀和液动换向阀组合而成,前者作为先导级以其出口压力来控制液动换向阀的正反向开口量的大小,从而控制液流方向和流量的大小,电液比例换向阀的工作原理如图5-5所示,先导级电液比例减压阀由两个比例电磁铁2、4和阀芯3组成,经通道a、b反馈至阀芯3的右端,与电磁铁2的电磁力平衡。因而减压后的压力与供油压力大小无关,而只与输入电流信号的大小成比例。减压后的油液经通道a、c作用在换向阀阀芯5的右端,使阀芯左移,打开A与B的连通阀口并压缩左端的弹簧,阀芯5的移动量与控制油压的大小成正比,即阀口的开口大小与输入电流信号成正比。如输入电流信号给比例电磁铁4,则相应地打开P与A的连通阀口,通过阀口输出的流量与阀口开口大小以及阀口前后压差有关,即输出流量受到外界载荷大小的影响,当阀口前后压差不变时,则输出流量与输入的电流信号大小成比例。
液动换向阀的端盖上装有节流阀调节螺钉1和6,可以根据需要分别调节换向阀的换向时间,此外,这种换向阀也和普通换向阀一样,可以具有不同的中位机能。
摆动式液压缸也称为摆动液压马达。当它通入压力油是,它的主轴能输出小于360°的摆动运动,常用于夹具夹紧装置、送料装置、转为装置以及需要周期性进给的系统中。图5-6(a)所示为单叶式摆动缸,它的摆动角度较大,可达300°。当摆动缸进出油口压力为p1与p2,输入流量为q时,它的输出转矩T和角速度ω各为
式中b是叶片宽度,R1,R2为叶片底部、顶部的回转半径。
图5-6(b)为双叶片式摆动缸,它的摆动角度较小,可达150°,它的输出转矩是单叶片式的两倍,而角速度则是叶片式的一半。
齿条传动液压缸结构形式很多,图5-7所示是一种用于驱动回转工作台回转的齿条传动液压缸。图中两个活塞4,7用螺钉固定在齿条5的两端、两端盖2和8通过螺钉、压板和半圆环3连接在缸筒上。当压力油从油口A进入缸的左腔时,推动齿条活塞向右运动,通过齿轮6带动回转工作台运动。液压缸右腔的回油经油口A排出。当压力油从油口B进入右腔时,齿条活塞向左移动,齿轮6反方向回转,左腔的回油经油口A排出。活塞的行程可由两端盖上的螺钉1,9调节,端盖2和8上的沉孔和活塞4上两端的凸头组成间隙式缓冲装置。
控制用的阀和驱动用的液压缸或液压马达组合起来形成液压伺服马达。液压伺服马达也可以看做把阀的输入位移转换成压力差并高效率地驱动载荷的驱动器。图5-8所示为滑阀伺服马达的原理。伺服马达有阀套和在阀套内沿轴线移动的阀芯,靠阀套上的五个口和阀肩的三个凸肩可实现,中部的供油口连接有一定压力的液压源,两侧的两个口接油箱,两个载荷口用 与驱动器相连。当供油口处于关闭状态,阀芯向右移动(x>0时),供油压力为sp。经过节流口从左通道流到驱动器活塞左侧并以压力1p使载荷向右(y>0)移动,相反,阀芯向左移动(x<0时),压力2p的液压油供到活塞右侧,使载荷向左移动(y<0)
空气压缩机输出的压缩空气首先储存于储气罐中,然后供给各个回路使用 。 气动回路使用过的空气无需回收,而是直接经排气口排入大气,因而没有回收空气的回气管道。
气压驱动系统的组成与液压系统有许多相似之处,但在以下三个方面有明显的不同:
空气压缩机输出的压缩空气首先储存于储气罐中,然后供给各个回路使用 。
气动回路使用过的空气无需回收,而是直接经排气口排入大气,因而没有回收空气的回气管道
图5-9为一典型的气压驱动回路。在这个图中没有画出空气压缩机和储气罐。压缩空气由空气压缩机产生,其压力约为0.5-0.7Mpa,并被送入储气罐。然后由储气罐用管道接入驱动回路。在过滤器内出去灰尘和水分后,流向压力调整阀调压,使空气压缩机的压力至4-5Mpa。
在油雾器中,压缩空气被混入油雾。这些油雾用于润滑系统的滑阀及气缸,同时也起一定的防锈作用。
从油雾出来的压缩空气接着进入换向阀,电磁换向阀根据电信号,改变阀芯的位置使压缩空气进入气缸A腔或者B腔,驱动活塞向右或者向左运动。
一般规定,当排气量大于或等于6-123/minm的情况下,就有必要单独设立压缩空气站。压缩空气站主要由空气压缩机、吸气过滤器、后冷却器、油水分离器和储气罐组成。如要求气体质量更高,还应附设气体的干燥、净化等处理装置。
空气压缩机种类很多,主要有活塞式、叶片式、螺杆式、离心式、轴流式、混流式等。前三种为容积式,后三种为速度式。
所谓容积式就是周期地改变气体容积的方法,即先通过缩小空气的体积,使单位体积内气体分子密度增加,形成压缩空气。而速度式则是先让气体分子得到一个很高的速度,然后让他停滞下来,将动能转化为静压能,使气体的压力提高。
选择空气压缩机的基本参数是供气量和工作压力。工作压力应当和空气压缩机的额定排气压力相符,而供气量应当与所选压缩机的排气量相符。
气源净化辅助设备包括后冷却器、油水分离器、储气罐、干燥器、过滤器等。
后冷却器安装在空气压缩机出口处的管道。它对空气压缩机排出的温度高达150℃左右的压缩空气降温,同时使混入压缩空气的水汽和油气凝聚成水滴和油滴。通过后冷却器的气体温度降至40-50℃。
后冷却器主要有风冷式和水冷式两种,风冷式冷却器如图5-10所示。风冷式冷却器是靠风扇产生的冷空气吹向带散热片的热气管道来降低压缩空气温度的。它不需要循环冷却水,所以具有占地面积小,使用及维护方便等特点。
油水分离器的作用是分离压缩空气中凝聚的水分、油份和灰尘等杂质,使压缩空气初步得到净化,其结构形式有环形回转式、撞击折回式、离心旋转式、水浴式及以上形式的组合等。撞击折回式油水分离器结构如图5-11所示。当压缩空气由进气管4进入分离器壳体以后,气流先受到隔板2的阻挡,被撞击而折回向下,之后又上升并产生环形回转,最后从输出管3排出。与此同时,在压缩空气中凝聚的水滴、油滴等杂质受惯性力的作用而分离析出,沉降于壳体底部,由阀6定期排出。
如图5-12 所示。储气罐的作用是储存一定量的压缩空气,保证供给气动装置连续和稳定的压缩空气,并可减小气流脉动所造成的管道振动。同时,还可进一步分离油水杂质。储气罐上通常装有安全阀、压力表、排污阀等。
如图5-13所示。为了进一步排除压缩空气中的水、油与杂志,以供给要求高度干燥、洁净压缩空气的气动装置。
如图5-14所示。对要求高的压缩空气,经干燥处理之后,再经过二次过滤。过滤器大致有陶瓷过滤器、焦炭过滤器、粉末冶金过滤器及纤维过滤器等。
气压驱动器时最简单的一种驱动方式,气体驱动元件有直线汽缸和旋转气动马达两种。气压驱动器除了用压缩空气作为工作介质外,其它与液压驱动器类似。气动马达和汽缸是典型的气压驱动器。气压驱动器结构简单、安全可靠、价格便宜。但是由于空气的可压缩性,精度和可控性较差,不能应用在高精度的场合。一种新型的气动马达,用微处理器直接控制的一种叶片马达,能携带215.6N的负载而又获得高的定位精度(1mm)。
①叶片式气动马达 由于空气的可压缩性,使得汽缸的特性与液压油缸的特性有所不同。因为空气的温度和压力变化时将导致密度的变化,所以采用质量流量比体积流量更方便。假设汽缸不受热的影响,则质量流量MQ与活塞速度v之间有如下关系。
式中R-气体常数,T-绝对温度,V-汽缸腔的容积;k-比热常数,p-汽缸腔内压力,A-活塞的有效受压面积。
可以看出在系统中,活塞速度与流量之间的关系不像式v=Q/A那样简单,气动系统所产生的力与液压系统相同,也可以用式F=A△p来表达。典型的气动马达有叶片马达和径向活塞马达,其工作原理与液压马达相同。气动机械的噪声较大,有时要按照消声器。图5-15所示为叶片式气动马达的结构。叶片式气动马达的优点是转速高、体积小、重量轻,其缺点是气动启动力矩较小。
图5-16所示为气压驱动器的控制原理,它由放大器、电动部件及变速器、位移(或转角)-气压变换器和气-电变换器等组成。放大器把输入的控制信号放大后去推动电动部件及变速器,电动部件及变速器把电能转化为机械能,产生线位移或角位移。最后通过位移气压变换器产生与控制信号相对应的气压值。位移气压变换器是喷嘴挡板式气压变换器。气-电变换器把输出的气压变成电量用作显示或反馈。
目前,谐波减速器是用于机器人关节传动的主要装置,其主要优点是传动比大、运转平稳、结构简单、传动效率高,是一种比较理想的传动装置。但由于其本身固有的结构特点(通过柔轮的弹性变形实现运动传递,具有过量的柔顺,过量的间隙) ,造成刚度不够,在传递载荷时弹性变形回差较大,影响了机器人末端执行器的定位精度和动态特性。而且随着使用时间的增长,其运动精度还会显著降低。因此,为保证机器人在周期性运动时的运动精度,用刚性大、回差小的精密传动装置代替刚性小的谐波传动,是机器人传动发展的需要。
80年代中期,日本出现了在双曲柄少齿差行星传动机构基础上完善起来的RV 传动机构,并由帝人公司成功研制出应用于机器人的摆线针轮RV 减速器,自1986年投放市场以来, 其独特的优越性能引起学术界的关注,系列产品也得到用户的青睐。由于它是机器人用减速器中刚性最高的低振动减速器,对提高机器人的运动精度和动态特性非常有利,而且还具有体积小、传动比大、承载能力大、运动精度高、传动效率高等优点,因而该传动装置不仅被机器人生产中使用,在机床行业也广泛采用。例如: 数控车床( N C)主轴分度; 加工中心( MC)的辅助机( ATC)的驱动等;工厂自动化( FA)领域及各种精密伺服系统的应用量也逐渐增多。日本生产的RV减速器均采用一级渐开线齿轮和一级摆线针轮传动,由于加工摆线针轮需要先进的专用设备,工艺系统复杂,且摆线针轮对加工误差敏感,为了得到小回差和使载荷均匀分布,制造精度要求很高,如果不具备大批量生产条件,产品成本非常高,而我国现有加工水平很难达到这种精度要求。
变厚齿轮RV 减速器采用一级渐开线齿轮传动和一级少齿差内啮合变厚齿轮传动,是针对驱动机器人关节的需要而开发的一种新型传动装置,由于首次成功地将变厚齿轮应用于减速器中,用它来代替RV 传动中的摆线针轮,使该减速器不但继承了RV减速器的体积小、传动比大、承载能力大、刚度大、运动精度高、传动效率高等优点,而且利用变厚齿轮的结构特点,通过设计调隙机构调整变厚齿轮的轴向位置,可以方便地调节其啮合侧隙,减小回差,实现精密传动。由于国内外对内啮合变厚齿轮设计理论及加工方法的研究资料甚少,严重阻碍了内啮合变厚齿轮在实际中的应用。因此,通过进一步完善该种齿轮的设计理论,并找出一种简单易行的加工方法,不需开发专用机床或改装设备,利用国内现有的设备就可以加工出高精度的内啮合变厚齿轮副,从而用较低的成本制造出自行设计的高精度变厚齿轮RV减速器,这对提高我国机器人的性能,促进我国机器人工业的发展,具有重要的意义。
RV 传动机构是在K-H-V 型行星轮系的基础上发展起来的一种较先进的传动机构。目前在工程上已广泛采用的渐开线少齿差行星传动、摆线针轮行星传动均属K-H-V 型行星传动。一般的K-H-V 型少齿差行星传动机构具有传动比大、结构紧凑、体积小、重量轻等优点,因而得到了广泛的应用。该种传动装置通常都带有W输出机构,行星齿轮既作公转运动又作自转运动,公转运动是减速器的输入运动,自转运动是输出运动,两者又汇集在行星轮上,如图1所示。W输出机构的型式有双万向联轴节式、十字滑块式、浮动盘式、平行四边形机构式、孔销式和零齿差式等,其结构各异,功能却是相同的。但它们都存在程度不同的缺点,如使减速器结构复杂、工艺性差、结构尺寸增大、动态性能低劣和机械效率降低等, 此外,这种机构刚度低、附加动载荷大,特别是传递较大功率时,振动和噪声大,严重影响了这种传动的应用和推广。
基于上述问题,国内外学者进行了深入广泛的研究,在K-H-V 型行星齿轮传动的基础上又发展出双曲柄式少齿差行星传动机构,其指导思想就是将输入运动和输出运动分别由中心轮和行星轮承担,如图2所示。
这样,一方面省去了输出机构W, 避免了由它所带来的弊病,另一方面用一个平行四边形机构(双曲柄)代替转臂H ,设置了同步啮合的定轴齿轮副,经减速后再将运F动输送给少齿差轮系,这样可获得更大的速比,使机构更为紧凑和有效; 当总速比相同时,动轴上齿轮的速度较低、运转比较平稳、动载荷和噪音较小。通过对浮动盘、双曲柄式和销轴式三种型式的一齿差减速器进行对比试验表明,无论是效率的理论计算或实测值,双曲柄式少齿差行星减速器均为最高,并且噪音低,运转平稳。
我国太原工学院的朱景梓教授所提出的双曲柄少齿差减速器,其传动原理与日本的RV 减速器相同,不同之处是其齿形为渐开线齿形。双曲柄式少齿差行星减速器的理论分析和实验研究工作在1985年即已完成,并于同年在太原工学院机械厂试制出第一台样机。1983年,天津卷扬机厂成功地把输入功率为7. 5 kW的双曲柄式二齿差减速机应用于该厂生产的一吨快速卷扬机上,1989年,天津职业技术师范学院与天津减速机厂合作开发了双曲柄摆线针轮减速器,并获国家专利。同年,上海减速机厂从日本进口动力用RV 减速机并加以仿制。1990年,华东化工学院与天津职业技术师范学院共同研制双曲柄式渐开线行星减速器,并应用在北京人民机器厂生产的P-880型双开四色胶印机上。
在国外, RV 减速器的研制、生产主要在日本。1961年,日本即开始从事三曲柄式行星传动行走装置的开发和生产。这种传动具有刚性高、超负荷能力强等优点,获得日本机械振兴协会的奖励。1983年,日本又开始进行高刚性、高精度、低振动的机器人用传动装置(即RV 传动机构)的研究,并于1986年日本帝人公司推出的偏心差动式RV系列减速机获得日本专利。它是一种两级减速机,一级为渐开线直齿轮减速部分,二级为三轴式摆线针轮行星减速部分。由于它具有减速比大、易改变速比、扭转刚度大、传动效率高、振动低、体积小等其它类型减速器所不可比拟的优点,因而已广泛应用于机器人的生产中。1986年投入市场,目前的生产厂家有帝人精机、三菱和住友株式会社等。同年,日本专利局公开了日本住友重机械公司研制的应用在油压机上的RV 减速机专利。70年代,西德Ch risho lm-Moo re制造公司生产的两种起重用卷扬机也采用了双曲柄少齿差行星传动机构。1986年,法国专利局也公布了一种与RV 传动机构类似的摆线齿形、渐开线齿形两种行星减速机专利。
综上所述,在双曲柄式少齿差行星传动机构基础上发展起来的RV 系列减速机具有许多独特的性能,适应现代机械发展的要求,是少齿差行星传动的一个新的发展方向。
RV传动是由一级行星传动部分和偏心差动式少齿差传动部分组合而成的二级减速传动。如图3所示,输入齿轮轴通过直齿轮(太阳轮)将电机的回转运动传递给二个均布的行星轮,实现第一级减速传动。行星轮通过曲轴H ,使摆线针轮做偏心运动。当机壳固定时,摆线针轮绕针轮一边公转一边自转,通过输出圆盘输出其自转运动,实现第二级减速传动。
从式( 4)中可以看出, 如果设法增大i1 ,就可以使共振时的输入转速转移到高速区域内。因此,可以防止低速区域的共振,从而减小振动。该RV传动通过一级减速后,使第二级偏心差动部分的输入转速大大降低,即偏心差动部分的离心惯性力得到降低,附加动载荷明显减小,相应地降低了附加动载荷引起的振动和噪声。同时,该RV减速器采用偏心圆盘输出机构,少齿差内齿啮合齿数多、抗过载能力强、扭转刚度大,可实现高刚度,耐冲击的传动。
( 2) 传动比范围。由式( 2)可知,固定针轮齿数z4的值,通过改变一级传动的齿轮副齿数z1 和z 2 ,就可方便地获得较大范围的传动比,易形成产品系列。
( 3) 效率和传递功率。RV 传动由太阳轮输入,经行星轮形成功率分流,由支撑圆盘输出。同时, RV 传动避免了少齿差传动输出机构的各种弊端,因而可实现高效率,大功率传动。
( 4) 扭转刚度与回差。RV 传动的摆线针轮z 3由中心圆盘支承的两个曲柄轴同时驱动,并通过中心圆盘直接输出。同时,少齿差传动部分啮合齿数多,所以整个传动装置抵抗变形能力强,弹性变形小,具有较高的扭转刚度,由弹性变形引起的回差小。
( 5) 体积和重量。RV 传动采用中心圆盘支承,内部采用超薄主轴承,使轴向尺寸大大减小。
因而结构紧凑、体积小、重量轻,很适合机器人关节传动。
由于RV 传动装置具有上述优点,因此其用途是很广泛的。它不仅适用于机器人传动,而且还可以用于机床领域、起重运输、印刷机械、轻纺机械以及其他机械化、自动化领域中的精密传动。
目前,机器人关节驱动装置主要是谐波减速器和RV减速器。但是,由于谐波减速器本身固有的缺点,使其在传递载荷时产生较大的弹性变形和回差,影响了机器人末端执行器的定位精度和动态特性。因此,用运动精度高、刚度大、回差小、振动低的RV 减速器代替国内机器人关节常用的谐波减速器,是我国机器人产业发展的必然趋势。
在国外,尤其是在日本,其先进的机器人关节都已采用RV减速器来驱动。而在国内,在国家863基金的资助下,已经研制出了高精度的变厚齿轮RV减速器。虽然由于国内加工水平的限制,各零部件的加工精度没有达到要求,但其多数主要性能指标仍然超过了日本同类产品的水平,如其间隙回差为47arc. sec (日本为1) ; 扭转刚度为134. 53N· m· arc /min- 1 (日本为78 N· m·a rc /min- 1 ) ; 传动效率为91. 95% (日本为85% )。可以看出,其主要性能指标达到了国际先进水平,并且价格仅为日本同类产品的三分之一,完全可以取代日本的RV 减速器,实现该类产品的国产化,并可以作为谐波减速器的更新换代产品,满足我国机器人工业生产的需要。
机器人电动伺服驱动系统是利用各种电动机产生的力矩和力,直接或间接地驱动机器人本体以获得机器人的各种运动的执行机构。
对工业机器人关节驱动的电动机,要求有最大功率质量比和扭矩惯量比、高起动转矩、低惯量和较宽广且平滑的调速范围。特别是像机器人末端执行器(手爪)应采用体积、质量尽可能小的电动机,尤其是要求快速响应时,伺服电动机必须具有较高的可靠性和稳定性,并且具有较大的短时过载能力。这是伺服电动机在工业机器人中应用的先决条件。
1)快速性。电动机从获得指令信号到完成指令所要求的工作状态的时间应短。响应指令信号的时间愈短,电伺服系统的灵敏性愈高,快速响应性能愈好,一般是以伺服电动机的机电时间常数的大小来说明伺服电动机快速响应的性能。
2)起动转矩惯量比大。在驱动负载的情况下,要求机器人的伺服电动机的起动转矩大,转动惯量小。
3)控制特性的连续性和直线性,随着控制信号的变化,电动机的转速能连续变化,有时还需转速与控制信号成正比或近似成正比。
4)调速范围宽。能使用于1:1000~10000的调速范围。
6)能经受得起苛刻的运行条件,可进行十分频繁的正反向和加减速运行,并能在短时间内承受过载。
目前,由于高起动转矩、大转矩、低惯量的交、直流伺服电动机在工业机器人中得到广泛应用,一般负载1000N(相当100kgf)以下的工业机器人大多采用电伺服驱动系统。所采用的关节驱动电动机主要是AC伺服电动机,步进电动机和DC伺服电动机。其中,交流伺服电动机、直流伺服电动机、直接驱动电动机(DD)均采用位置闭环控制,一般应用于高精度、高速度的机器人驱动系统中。步进电动机驱动系统多适用于对精度、速度要求不高的小型简易机器人开环系统中。交流伺服电动机由于采用电子换向,无换向火花,在易燃易爆环境中得到了广泛的使用。机器人关节驱动电动机的功率范围一般为0.1~10kW。工业机器人驱动系统中所采用的电动机,大致可细
(1)交流伺服电动机 包括同步型交流伺服电动机及反应式步进电动机等。
(2)直流伺服电动机 包括小惯量永磁直流伺服电动机、印制绕组直流伺服电动机、大惯量永磁直流伺服电动机、空心杯电枢直流伺服电动机。
(3)步进电动机 包括永磁感应步进电动机。 速度传感器多采用测速发电机和旋转变压器;位置传感器多用光电码盘和旋转变压器。近年来,国外机器人制造厂家已经在使用一种集光电码盘及旋转变压器功能为一体的混合式光电位置传感器,伺服电动机可与位置及速度检测器、制动器、减速机构组成伺服电动机驱动单元。 机器人驱动系统要求传动系统间隙小、刚度大、输出扭矩高以及减速比大,常用的减速机构有:
工业机器人电动伺服系统的一般结构为三个闭环控制,即电流环、速度环和位置环。 目前国外许多电动机生产厂家均开发出与交流伺服电动机相适配的驱动产品,用户根据自己所需功能侧重不同而选择不同的伺服控制方式,一般情况下,交流伺服驱动器,可通过对其内部功能参数进行人工设定而实现以下功能:
(PWM)伺服驱动器,通过改变脉冲宽度来改变加在电动机电枢两端的平均电压,从而改变电动机的转速。
PWM伺服驱动器具有调速范围宽、低速特性好、响应快、效率高、过载能力强等特点,在工业机器人中常作为直流伺服电动机驱动器。
同直流伺服电动机驱动系统相比,同步式交流伺服电动机驱动器具有转矩转动惯量比高、无电刷及换向火花等优点,在工业机器人中得到广泛应用。
同步式交流伺服电动机驱动器通常采用电流型脉宽调制(PWM)相逆变器和具有电流环为内环、速度环为外环的多闭环控制系统,以实现对三相永磁同步伺服电动机的电流控制。根据其工作原理、驱动电流波形和控制方式的不同,它又可分为两种伺服系统:
采用矩形波电流驱动的永磁交流伺服电动机称为无刷直流伺服电动机,采用正弦波电流驱动的永磁交流伺服电动机称为无刷交流伺服电动机。
步进电动机是将电脉冲信号变换为相应的角位移或直线位移的元件,它的角位移和线位移量与脉冲数成正比。转速或线速度与脉冲频率成正比。在负载能力的范围内,这些关系不因电源电压、负载大小、环境条件的波动而变化,误差不长期积累,步进电动机驱动系统可以在较宽的范围内,通过改变脉冲频率来调速,实现快速起动、正反转制动。作为一种开环数字控制系统,在小型机器人中得到较广泛的应用。但由于其存在过载能力差、调速范围相对较小、低速运动有脉动、不平衡等缺点,一般只应用于小型或简易型机器人中。
步进电动机所用的驱动器,主要包括脉冲发生器、环形分配器和功率放大等几大部分,其原理框图如图2所示。
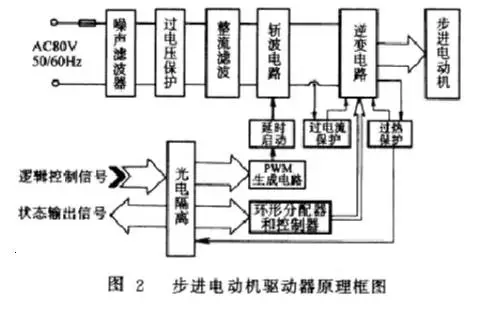
所谓直接驱动(DD)系统,就是电动机与其所驱动的负载直接耦合在一起,中间不存在任何减速机构。
同传统的电动机伺服驱动相比, DD驱动减少了减速机构,从而减少了系统传动过程中减速机构所产生的间隙和松动,极大地提高了机器人的精度,同时也减少了由于减速机构的摩擦及传送转矩脉动所造成的机器人控制精度降低。而DD驱动由于具有上述优点,所以机械刚性好,可以高速高精度动作,且具有部件少、结构简单、容易维修、可靠性高等特点,在高精度、高速工业机器人应用中越来越引起人们的重视。 作为DD驱动技术的关键环节是DD电动机及其驱动器。它应具有以下特性:
1)输出转矩大:为传统驱动方式中伺服电动机输出转矩的50~100倍。
2)转矩脉动小: DD电动机的转矩脉动可抑制在输出转矩的5%~10%以内。
3)效率:与采用合理阻抗匹配的电动机(传统驱动方式下)相比, DD电动机是在功率转换较差的使用条件下工作的。因此,负载越大,越倾向于选用较大的电动机。 目前,DD电动机主要分为变磁阻型和变磁阻混合型,有以下两种结构型式: l)双定子结构变磁阻型DD电动机; 2)中央定子型结构的变磁阻混合型DD电动机。
1)压电驱动器。众所周知,利用压电元件的电或电致伸缩现象已制造出应变式加速度传感器和超声波传感器,压电驱动器利用电场能把几微米到几百微米的位移控制在高于微米级大的力,所以压电驱动器一般用于特殊用途的微型机器人系统中。
3)真空电动机,用于超洁净环境下工作的真空机器人,例如用于搬运半导体硅片的超真空机器人等。
来源:萝卜库
Alphabet新动向:正在利用人工智能“专致”蚊子不孕不育
雅虎开发“智能”广告牌:可以通过摄像头和麦克风捕捉人们的看法
谷歌在纽约为自家硬件产品开设了一家快闪实体店
我国智能仓储业将引入机器人
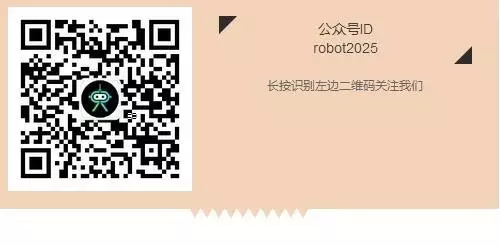
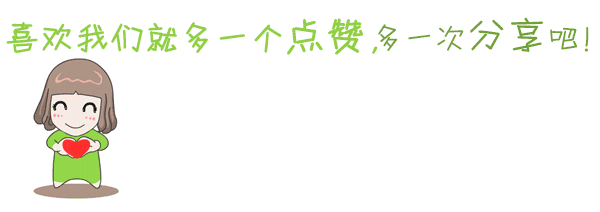
转载自blog.csdn.net/cgy8919/article/details/53186020